Air compressors are an essential part of most industrial facilities by providing the compressed air to operate pneumatic instruments, control valves, and processes. Airborne contaminants at these industrial facilities, such as refineries, pulp & paper mills, and chemical plants, are typically derivatives of sulfur and chlorine. These corrosive gases
become entrained in the compressed air and create an acidic condensate which attacks metal surfaces, leads to increased vibration, and causes loss of compressor efficiency. MAS can measure the acidity of contaminated condensate and identify if sulfur or chlorine compounds are causing the increase in pH.
Armed with the proper data, proper actions can be taken to ensure contaminants, both gaseous and particulate, are removed from the intake airstream allowing compressors run properly, with a long service life and minimal repairs.
The benefits of the controlling acidic condensate include:
• Eliminate vibrations caused by buildup of corrosion by-products and prevent corrosion damage to intercoolers, diffusers and casings.
• Protect the process from contamination.
• Prevent the loss of cooling due to corrosion of intercooler.
• Allow for the use of standard copper intercooler tubes even in a contaminated atmospheres.
• Eliminate unnecessary repair costs by extending operating hours between servicing.
• Reduce initial cost of compressor and allow for use of less costly, standard replacement parts.
Understand the cause of your Breakdowns!
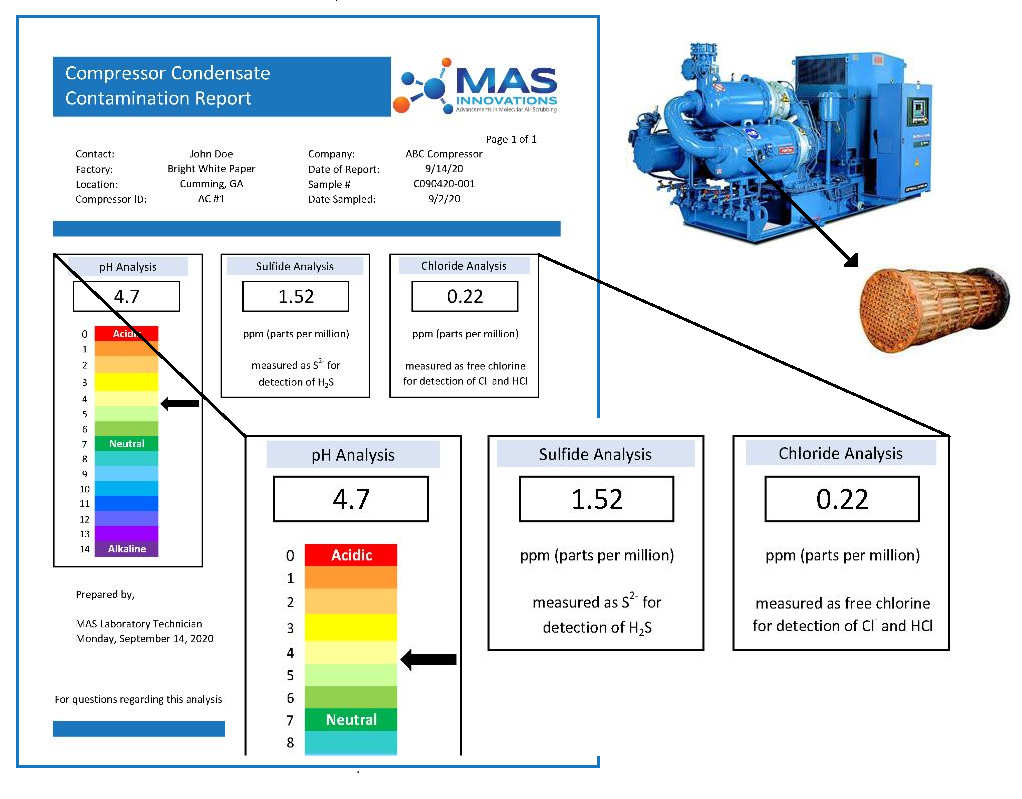