Corrosion of electronics due to ambient air pollution has been documented for many years. The problem is prevalent at heavy industrial sites such as pulp and paper mills, petrochemical refineries, and chemical plants. These industrial facilities produce local environments that are relatively high in sulfur content – hydrogen sulfide, sulfur dioxide, mercaptans, or sulfur laden particulates. Therefore, circuit boards in these plants are subject to corrosion due to reactions with the ambient sulfur.
In 2003, the European Union passed the Restriction of Hazardous Substances (RoHS) Directive and its requirements have caused many electronic equipment manufacturers to change materials to ones much more susceptible to gaseous corrosion. These types of connections can fail quickly even in moderate environments, previously thought to cause problems only after long periods of exposure.
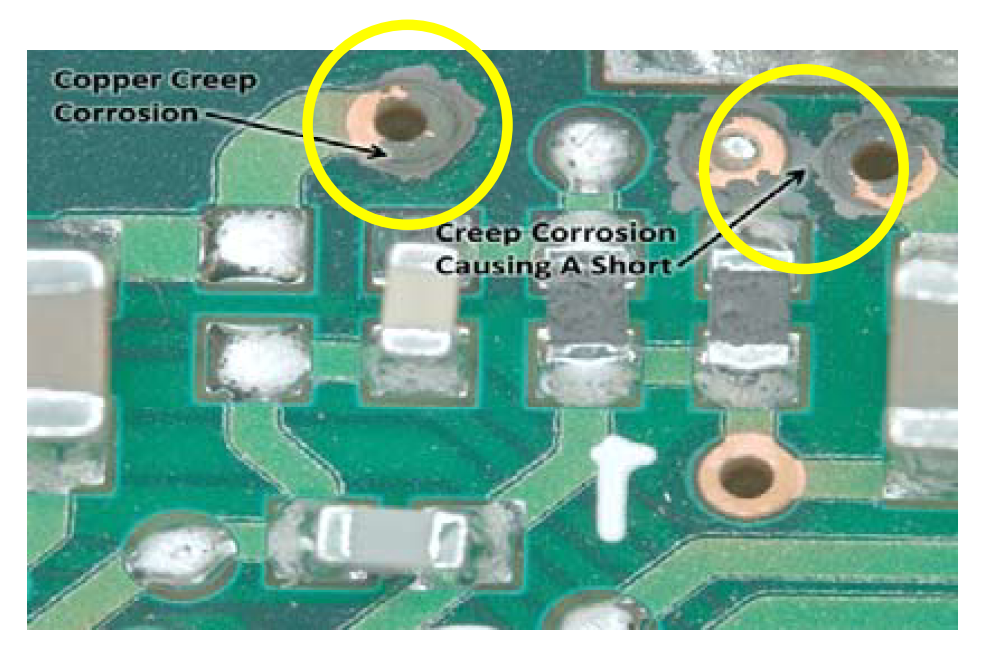
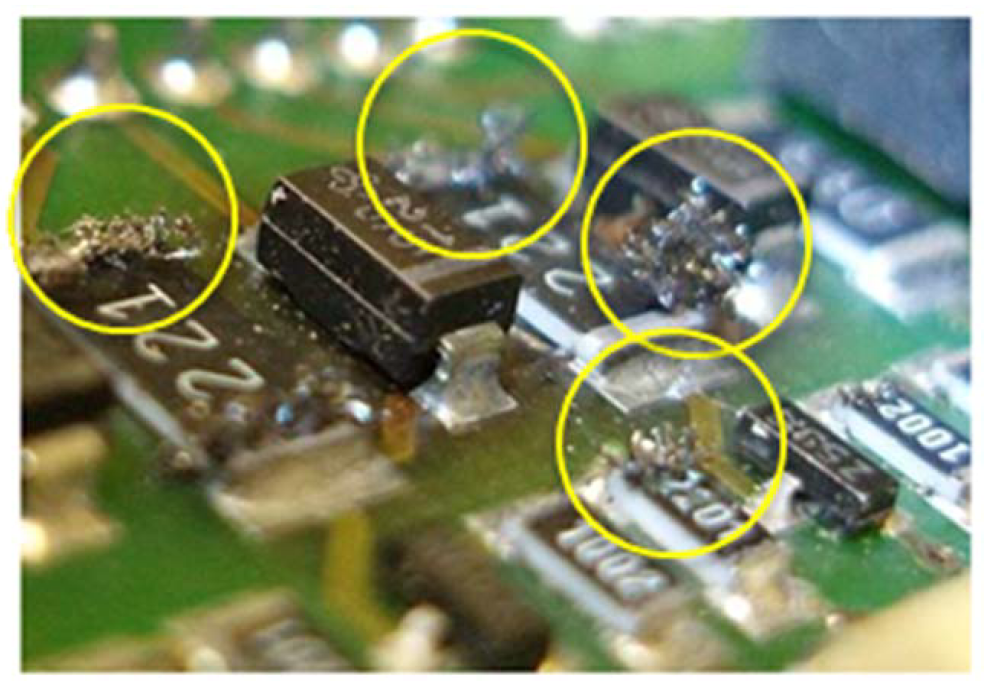
There are several types of electronic circuitry corrosion including whisker growth and creep corrosion. These forms of corrosion can cause failure by either impeding the flow of electricity or forming unintended circuit paths. Figure 2 displays an example of silver whisker growth on surface mounted components of a circuit board. It will cause failures by forming unintended circuit paths on the circuit board. The growth of silver whiskers is the notable indicator to server manufacturers that sulfur contamination is in the presence of their equipment.
MAS Innovations understands the need to provide gas-phase and particulate filtration systems for mission control facilities. Employing such systems can:
- Eliminate process shutdown due to control equipment failures
- Maintain high process efficiency
- Extend circuit board life and reduce electronics’ replacement costs
- Document corrosion levels in control rooms
- Help protect warranty claims
Classification | Å/30 days | Description | |
Copper | Silver | ||
G1 Mild | <300 | <200 | Environment sufficiently controlled. |
G2 Moderate | <1000 | <1000 | Corrosion may lead to failure. |
G3 Harsh | <2000 | <2000 | High probability of failure. |
GX Severe | >2000 | >2000 | Only hardened equipment survives |
Environmental Conditions for Control Rooms and Electronic Systems
With the miniaturization of electronics, electrical components are decreasing in size and circuit board density is increasing. Today’s electronics have an increased heat load and require more airflow to prevent overheating. Difficulty in sealing the electrical components and protecting them from environmental conditions and molecular contamination can lead to failures.
In response to these problems, a standard was developed to classify control rooms and process control environments (see Table 2). Most equipment manufacturers require that the control room environment meet the ISA G1 –
Mild classification to maintain a reliable communication network in industrial
environments. The only way to meet this requirement in many industrial environments is to protect the control room with chemical and particulate filtration.
Most electronics manufacturers require their equipment to be housed in an environment that has a copper corrosion rate less than 300 Å/month and a silver corrosion rate less than 200 Å/month. Equipment warranties may be voided if an environment is not sufficiently filtered such that corrosion will not be a factor in equipment’s reliability.
Utilize MAS’s Equipment Reliability Program (ERP) where our local representatives can monitor and maintain your chemical scrubbers while
documenting control room corrosion levels and physical integrity.
The heart of any gas phase scrubber is its chemical media/ catalyst. Media selection is critical to the efficiency and longevity of the scrubber’s life. Scrubber designs can employ multiple media passes with layers of protection or a single, blended media bed.
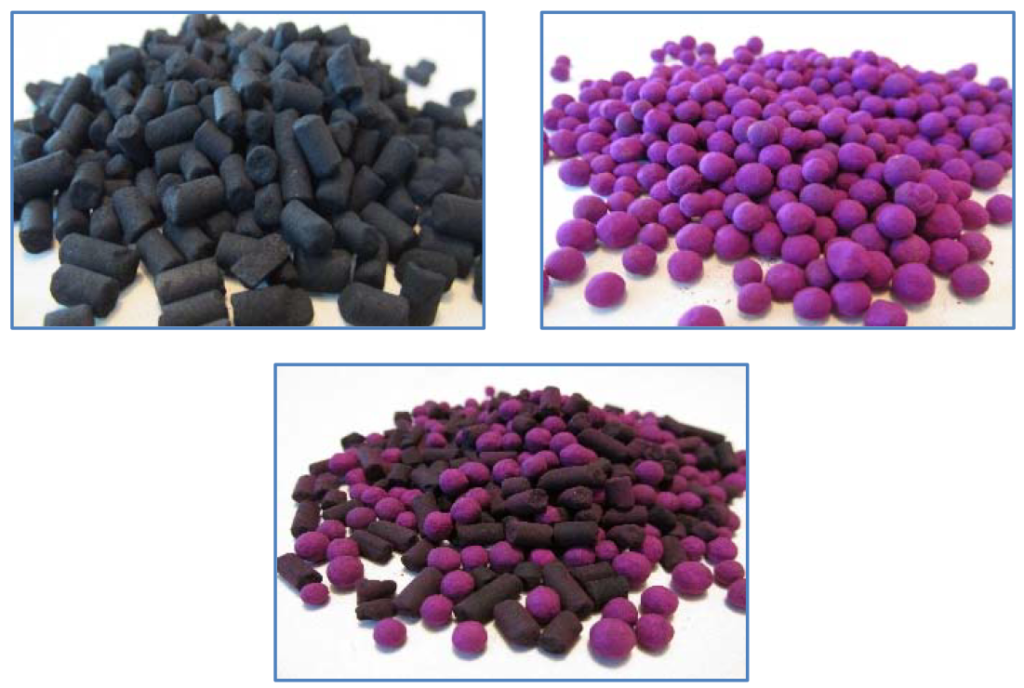
Gaseous Contamination and Control
Sulfur-bearing gases, such as sulfur dioxide (SO2) and hydrogen sulfide (H2S), are the most common gases that cause corrosion on electronic equipment. A very convenient and quantitative way to determine the corrosivity of an environment is called “reactivity monitoring”, a method described in ISA-71.04. This method exposes copper and silver coupons to the environment for thirty days, analyzes the corrosion films’ thickness using coulometric reduction, and then correlates the results into their corrosion level. The corrosion films can help identify sulfur or chlorine contaminants.
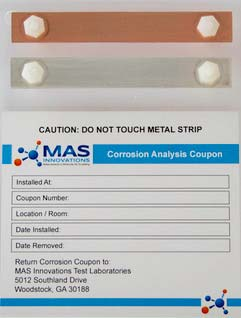
Corrosion Coupon with Copper and Silver
The most susceptible components on circuit boards are made with copper and silver. Corrosion monitoring with both copper and silver coupons provides better insight as to how your equipment will withstand the affects of your environment.
Particulate Contamination and Control
Failures due to dust are generally classified as:
- Mechanical effects include obstruction of cooling airflow, interference of moving or optical parts, and deformation of surfaces.
- Chemical effects include corrosion of electrical components due to dust comprised of sulfur and chlorine-bearing salts.
- Electrical effects include impedance changes and electronic circuit conductor bridging.
Fine dust particles can stay airborne for years. Origins can be fossil-fuel burning, volcanic activity, forest fires, humidifier feed water, or sea salt spray.
Failures are accelerated when the dust absorbs moisture. When wetted, dust can more easily contribute to corrosion and ion migration. Air recirculated within a computer room should be filtered with a MERV 8 filtration. Outside air
brought into the computer room should be filtered with MERV 11 or MERV 13 filtration.
Air Handling Techniques for Mission Critical Facilities
Protection of a computer and server rooms starts with pressurization using purified air. This prevents corrosive gases from infiltrating the protected area
and causing corrosion problems. Pressurization is a key requirement as contaminants will always seek equilibrium with low concentration areas.
Additionally, recirculation air may require cleaning if the room is a high traffic area or has internal sources of contaminants.
Equipment for Corrosion Control
Side Access Housing (SAH)
Side Access Housings are designed to support chemical media cassettes, pre-filters, after-filters, and high efficiency particulate filters in one self-contained unit for the removal of gas-phase contaminants and airborne particulate. SAHs allows for maximum customization in the amount of air volume that can be treated and the types of chemical and particulate filter elements that can be used to remove contaminants.
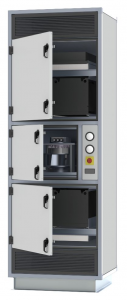
Air Filtration Unit (AFU)
Air Filter Units are stand-alone, multi-stage systems designed to remove particulate and gaseous contaminants from small computer rooms and MCCs.
AFUs are double-wall insulated construction to reduce noise and thermal transfer. The scrubber can be used to recirculate air directly from the control room and return the purified air to the control room. Alternatively, the scrubber can be customized to draw both outdoor air and room air providing a purified mixed air stream. Adding outdoor air pressurizes the control room and prevents contaminants from infiltrating the space.
Tub Scrubber (TS)
Tub Scrubbers are ideal to treat a small amount of heavily contaminated air and where high level of particulate filtration is needed. The scrubbers are designed with a deep (36-inch) bed for long service life, typically two-three years. The vertical airflow design minimizes the equipment’s footprint. Airflows for the Tub Scrubber range from 500 to 4000 cfm.
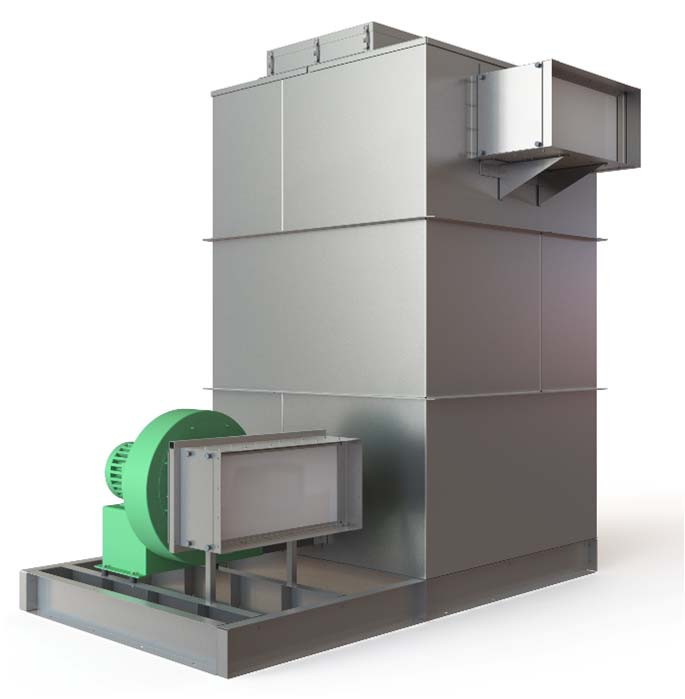
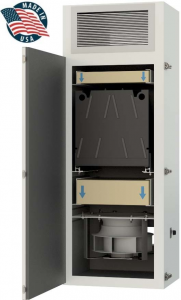
Electronic Cabinet Unit (ECU)
Electronic Cabinet Units are small single-stage systems designed to remove particulate and gaseous contaminants from individual or remote electrical cabinets. The small design with an airflow capacity of 100-500 cfm allows the scrubber to be attached directly onto the control panel. A manual damper allows air to be recirculated within the control cabinet or drawn from outside the cabinet creating purified pressurization air to prevent infiltration of contaminants.